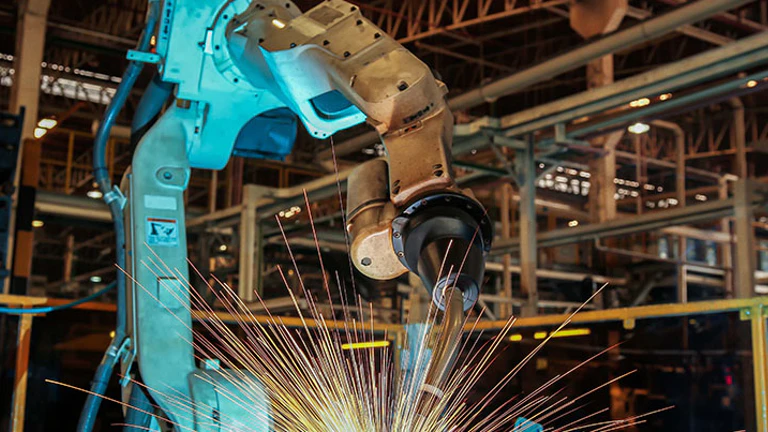
An Outlook Survey issued by the National Association of Manufacturers early last year confirmed that many company’s executives are finding it challenging to find skilled workers for their manufacturing applications. Another survey by the Society of Manufacturing Engineers (SME) confirmed these findings when it interviewed various manufacturers. SME found that about 89 per cent of manufacturers can’t find enough skilled workers to fill their manufacturing jobs.
We don’t expect the situation to change any time soon. According to Deloitte, more than 4.6 million employment opportunities will be created by manufacturing over the next decade, but nearly half of them will go unfulfilled. These shortages have been felt across all industries. Manufacturers on their part are doing anything humanly possible to address the skills shortage in the manufacturing industry.
Some company’s executives have turned to measures such as assigning more overtime, recruiting temporary staff, and encouraging retirees to hang in for a little longer. Such drastic measures taken to keep the company running can hurt the business. Some companies have been forced to turn away new business because they don’t have the right workforce for the job. Most of the businesses are likely to close shop in this decade if they don’t address workforce constraints.
What’s the Solution?
To address the shortage of skilled labour in manufacturing industries, many executives are turning to automation. However, some small and medium-sized manufacturing companies cannot implement automation in their production process due to the lack of relevant technical skills.
Most of these challenges can be addressed by using collaborative robots, which is the fastest-growing segment in the robotics industry. Many companies are embracing the use of collaborative robots because they are flexible, easy to integrate, low cost, small footprint, and they can work safely alongside human workers. These attributes make them attractive for both small- and large-scale manufacturers.
Use of collaborative robots is also helping manufacturers to meet the changing consumer demands. Modern consumers are looking for highly customized and innovative products, and this is what cobots offer. Many manufacturers prefer collaborative robots because they allow companies to have smaller production lines and also to build multiple alternative models.
Cobot Modernize Manufacturing
Industrial robots were introduced in the 19770s. They were mainly designed to improve productivity and speed. The first robots were expensive to purchase and install. They also required the installation of safety systems that took up large spaces on the production floor. They also needed highly trained technicians and engineers to program and keep them operating.
Cobots offers almost similar benefits to traditional robots. They can take over dirty, dangerous, and repetitive tasks that may be boring for human workers. Introduction of industrial robots led to the production of high-quality products, reducing scrap, and increasing yields. Cobots, on their part, also offer many new benefits to manufacturers than traditional robots.
Cobots feature artificial intelligence and machine learning attributes which help them to work safely alongside human workers. They are lightweight and have a small footprint, and hence can be used in any design of the production floor. Cobots have arms with a wide range of payload to meet various needs such as robotic machine tending, assembly, pick and place, and packaging.
New Developments in Cobot Manufacturing
The robotic industry is continuously coming up with innovations that are changing the manufacturing landscape. The introduction of end-of-arm tooling (EoAT) devices has added value to robot arms. These tools have enhanced the preciseness of the robotic machine tending process. Most of these tools used in robots are safe, user-friendly, and easy to install.
Introduction of EoAT devices such as changers allows technicians to swap out grippers on the production floor. This enhances flexibility since a single robot can be used to perform different tasks on the production floor. It also reduces time, cost, and effort needed to change a robot from one job to the other.
In this decade, many companies continue to seek ways to transform their business by leveraging the available technology. The machine-human pairing seems to provide the correct balance of cutting costs, improving quality and streamlining production.