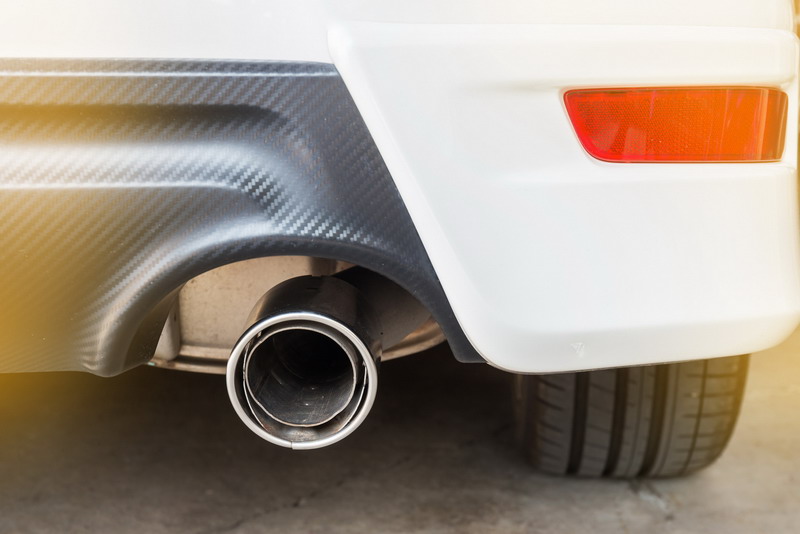
Composites like carbon fiber are used in a wide array of manufacturing processes these days. Composites are a big part of everything from airplanes to sporting goods. So why is it they have not caught on in the automotive industry? According to one expert, it is due to a lack of performance data.
Ford Motor Company’s Patrick Blanchard recently addressed the 2017 SPE Automotive Composites Conference and Exhibition, focusing on the integration of composite materials in auto manufacturing. Blanchard outlined three things that were preventing auto companies from using composites more than they do:
- Design optimization
- Forming simulation
Blanchard explained that design optimization is the number one challenge. He went on to say that performance data is key to design optimization, and that performance data is lacking in the composites arena. Before composites can be more widely adopted by car makers, performance data has to be improved.
Keeping up with the Design Cycle
At the core of the auto industry’s problem is the speed of the design cycle. In order to make mass-produced cars affordable on the American market, car companies have to be able to move new parts through the design cycle extremely quickly. They need to go from the design stage implementation more quickly than composites allow.
By contrast, a company like Salt Lake City’s Rock West Composites is not under such strict time constraints. They can take the time to develop new composite materials even as their current product list keeps the company going. They are not under the gun to produce new products quickly.
Blanchard told the SPE crowd that performance data associated with epoxy resin, carbon fibers, and other materials just isn’t there. Furthermore, standards for producing composite products are far from being settled. Therefore, automakers cannot look at reliable performance data to know how a composite material or epoxy resin will perform when fabricating a specific part. Nor do they have the time to find out.
By contrast, the performance data available for steel, aluminum, and plastics is available in almost overwhelming supply. Designers know exactly how a certain plastic is going to hold up to a particular application, so they know how to design new parts accordingly.
Time Is Money
To be clear, this is not to say that composite materials have no place in auto manufacturing. There are car companies already making use of composites. What it does mean is that use of composites adds to the price of the finished product to the extent that composites are not yet ready for prime-time mass production.
For the time being, composite materials will be used on high-end vehicles that will not be harmed by a higher price point. Think European sports cars if that helps. For the everyday family sedan coming off the Detroit assembly line though, the usefulness of composites is limited right now.
Make no mistake; the current problem is only going to be temporary. Carmakers know that composites provide more than enough strength while also reducing weight costs. They know the future of electric vehicles lies in the heavy use of composites, and they are hard at work trying to overcome the hurdles they now face. But it will take time.
In the meantime, Rock West Composites and other fabricators will continue doing what they do and providing critical performance data at the same time. The more they produce, the more data we will have to look at down the road. And when that performance data is there, auto makers will be a much better position to use composites more widely.